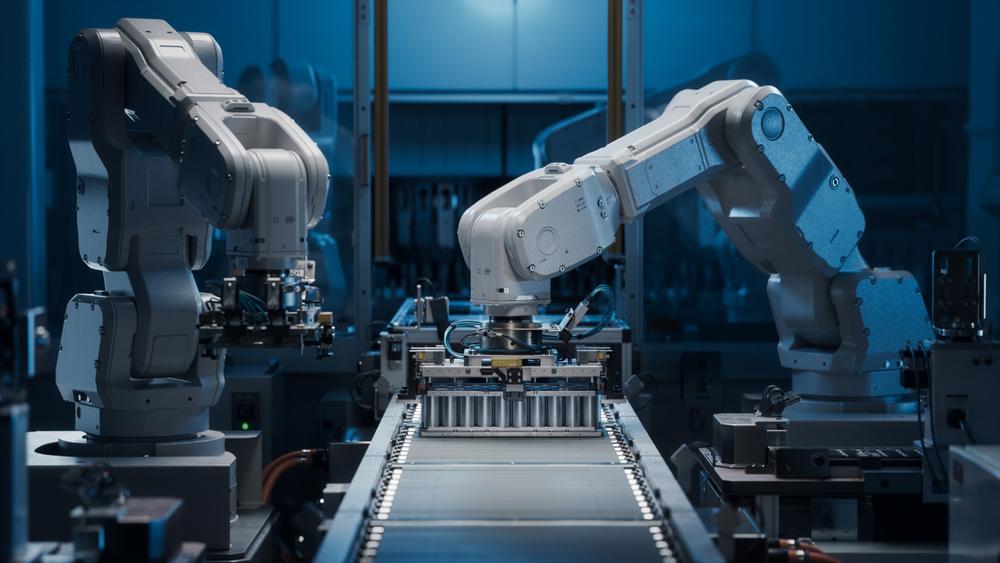
Case study: Bosch Diesel enhances project portfolio management with Easy Redmine
Manufacturing
2017
Jihlava, Czech Republic
4 400+
Project, Production, IT, Engineering
Bosch Diesel s.r.o., a subsidiary of the Bosch Group located in Jihlava, Czech Republic, operates one of the largest production plants for Common Rail diesel injection systems.
With over 4,400 employees and a facility valued at more than €700 million, efficient project management is crucial. Facing challenges with fragmented Excel-based planning, Bosch Diesel sought a comprehensive solution to streamline its project portfolio management.
Before switching to Easy Redmine
Before implementing Easy Redmine, project portfolio management at Bosch Diesel was spread across multiple disconnected Excel sheets. Project initiation, planning, and scheduling were all done manually and independently, often relying on the memory and diligence of individual project managers.
This fragmented system created serious bottlenecks. Planning was inefficient and prone to human error, especially during data transfers between documents. There was no unified way to assess available production capacity, making it difficult to balance workloads or predict when bottlenecks might occur.
As a result, projects were delayed and customer satisfaction dropped. Additionally, operational costs crept higher due to poor resource utilization and process duplication.
Project initiation, capacity planning, and scheduling were handled separately, leading to:
- Inefficient planning: Manual data transfer between sheets increased the risk of errors.
- Resource mismanagement: Difficulty in accurately assessing machinery and staff availability.
- Delayed deliveries: Inaccurate planning led to missed deadlines and customer dissatisfaction.
- High operational costs: Underutilization of resources and manual processes escalated expenses.
Solution: Easy Redmine on-premises implemented
To address these growing inefficiencies, Bosch Diesel began evaluating modern project management tools. The team considered solutions like Jira, Wrike, Asana, and Microsoft Project—but ultimately, Easy Redmine stood out for its native support for manufacturing workflows and its flexible deployment options.
Bosch Diesel was especially attracted to Easy Redmine’s capacity planning, visual dashboards, and integration capabilities. The system’s ability to be hosted on-premises using Docker also ensured that it met Bosch’s strict internal IT security requirements.
Implementation highlights:
- Data migration: Despite challenges with the legacy system lacking API support, data was successfully migrated via Excel imports.
- Customized deployment: Due to strict security policies, Easy Redmine was deployed using Docker containers, ensuring compliance and ease of updates.
- On-site training: Tailored workshops were conducted for project managers and executives to facilitate smooth adoption.
Results and benefits
After the rollout, Bosch Diesel reported a measurable transformation in how projects were initiated, tracked, and delivered. Project managers were finally equipped with real-time insights into capacity and timelines. The intuitive Gantt charts helped managers plan with greater precision, which in turn improved production scheduling and minimized conflicts.
Resource utilization improved significantly. By aligning attendance records with resource planning, the company was able to optimize the availability of both machinery and skilled personnel. This not only reduced overhead costs but also enabled project teams to take on more parallel projects without overstretching resources.
Moreover, the streamlined interface and central database improved communication across departments. Project data became more transparent, allowing cross-functional teams to collaborate more effectively and reduce planning cycles.
Post-implementation, Bosch Diesel experienced significant improvements:
- Enhanced Resource Management: Visual tools allowed for accurate planning and optimal utilization of machinery and personnel.
- Improved delivery accuracy: Reliable scheduling led to timely project completions and increased customer satisfaction.
- Increased efficiency: Automation reduced manual tasks, enabling managers to oversee more projects simultaneously.
- Better collaboration: Centralized information fostered teamwork and streamlined communication across departments.
The most-used features of Easy Redmine
Among the most impactful features for Bosch Diesel were the Project Portfolio Gantt, Resource Management, and Attendance Management modules.
The Project Portfolio Gantt feature enabled a bird’s-eye view of ongoing projects, providing clarity on dependencies, progress, and capacity. This allowed project leads to anticipate challenges before they became critical issues.
Resource Management tools allowed teams to assign and adjust workloads with real-time data, helping Bosch meet strict deadlines while maximizing staff efficiency.
Finally, Attendance Management integration ensured that project plans reflected the true availability of the workforce, making scheduling far more accurate and practical.
- Task & Project Management: Used for tracking projects and marketing campaigns.
- Custom Dashboards: Provides real-time visibility into ongoing activities.
- Reporting & Analytics: Helps in data-driven decision-making for both projects and marketing.
Conclusion: Bosch Diesel streamlines project management with Easy Redmine
By transitioning to Easy Redmine, Bosch Diesel transformed its project management approach, moving from fragmented Excel sheets to a unified, efficient system. The implementation led to better resource utilization, timely deliveries, and enhanced collaboration, solidifying Bosch Diesel’s position as a leader in manufacturing excellence.
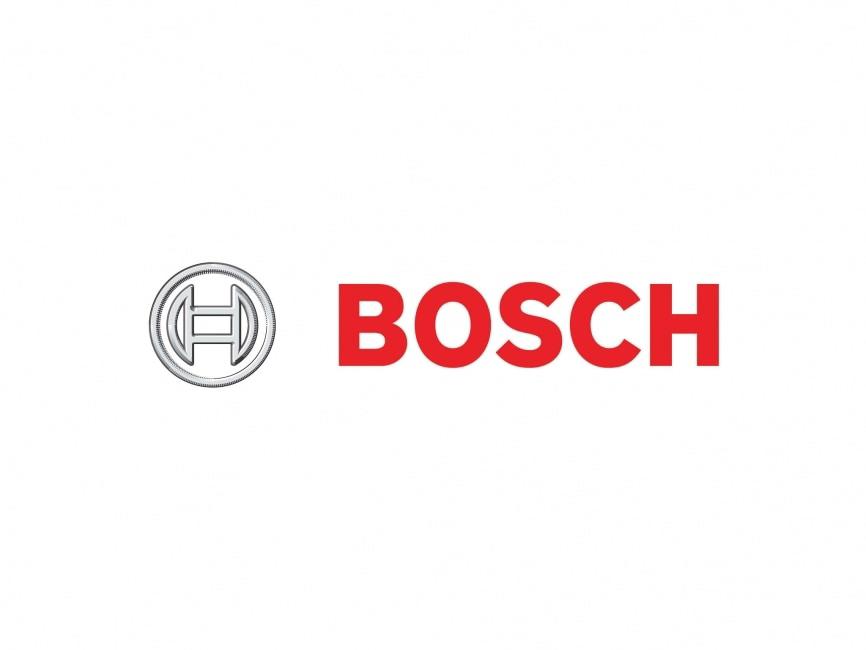
The most used functions
Customizable dashboard for HelpDesk
Customizable dashboard for tracking results
Automatically created milestones
Road map for managing the projects
Who is Bosch Diesel?
Bosch Diesel s.r.o. is a subsidiary of the global Bosch Group, operating one of the largest and most advanced production plants for diesel injection systems in Europe. Located in Jihlava, Czech Republic, the facility specializes in manufacturing Common Rail components used in modern diesel engines.
With a workforce of over 4,400 employees, Bosch Diesel plays a critical role in the automotive supply chain, delivering precision-engineered components to vehicle manufacturers worldwide. The company is known for its commitment to quality, innovation, and efficiency—values that are central to its continuous improvement initiatives.
Related case studies
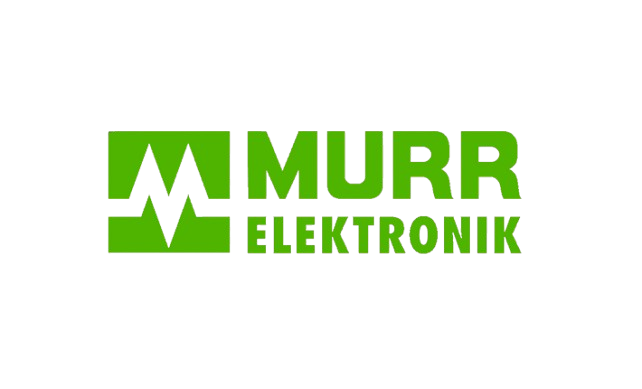
Case study of Murrelektronik: Streamlining complex project management with Easy Redmine
Decentralized Automation Manufacturer
Murrelektronik, a global leader in industrial automation solutions, faced growing complexities in managing large-scale projects across multiple departments and international teams.
To enhance visibility, streamline processes, and ensure timely project delivery, they required a flexible, robust solution—deployed on-premises to uphold stringent data security standards.
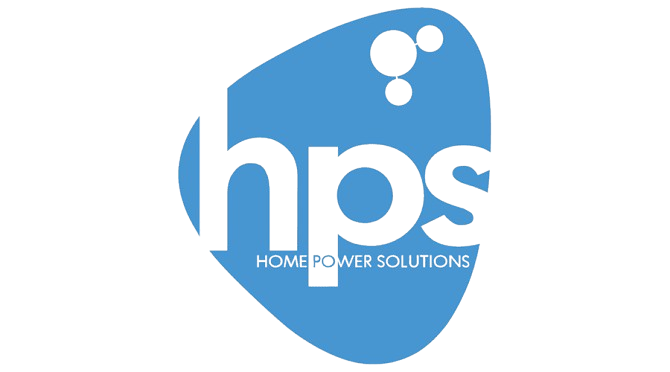
A Case Study of Home Power Solutions with Easy Redmine
Manufacturing
Discover the transformative impact of Home Power Solutions as they revolutionize sustainable living with innovative energy solutions, powered by Easy Redmine. This case study delves into Home Power Solutions' pioneering efforts to provide reliable and eco-friendly energy solutions for residential and commercial use.